”TMI” means Too Much Information for you people without teenagers in the family. You want to see how I felt about lunchtime today — the picture below is my brain on chairs. Day two of seven and we continue tomorrow with each student building their own Windsor chair, and I must admit I am a little intimidated.
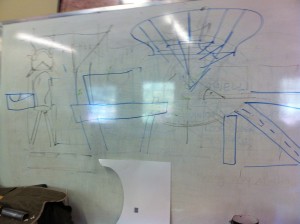
My Brain on Chairs
Today Peter finished putting his demonstration chair together. He started out this morning with digging out the seat and shaping it with the adze, scorp (is scorping a word?), travisher and any other thing he needed to make it work. He shaped the outside by sketching a line around the edge with a pencil and then making some pretty darn aggressive cuts with the drawknife. It didn’t take very long to make a lovely, symmetrical seat with hand tools only and just a few lines sketched on the seat. It was marvelous to watch. I’ll let you know how mine goes later in the week.
After the seat was almost finished, we watched Pete add the legs. We were only lacking the smoke because the mirrors were much in use and the way the stretchers go in, there is not much room for error. We spent a lot of time learning about making the mortises and tenons so they would fit together tightly.
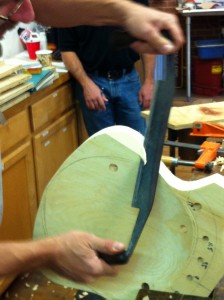
Shaping the Seat
After the seat was legged up, Pete moved on to the back and the spindles. Remember we bent the bow yesterday and it was in the form overnight, so he shaved the ends gently and precisely and then mounted it in place. After that, he moved on to installing the spindles. With some sweet little tricks for getting the lengths correct and drilling the holes in the bow in the right direction, all it needed was wedges to hold it together for the next 200 years, and a lot of finishing. We can talk about milk paint later in the week.
In the meantime, I have been collecting cool techniques and sayings from Pete (born in Atlanta, but currently living in New York State) and from other chair makers he knows around the country. Try these:
When he finishes sharpening his draw knife, he strops it on the end grain of the pine seat as the last step. (Maybe one day when I am 110 years old I will get where my draw knife needs stropping on a piece of soft pine.)
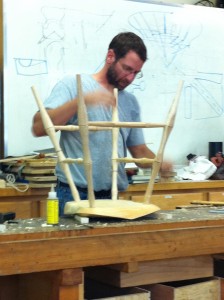
Legs Almost Ready
Go past the edge now and then so you will know where the edge is.
When you can turn really well and get a great finish with the tool, it will be so smooth you will have to sand the part so it will accept finish. (I should get so good.)
We only sand what we don’t understand.
There is a reason we call it abrasive.
Wish me luck!! See you tomorrow.
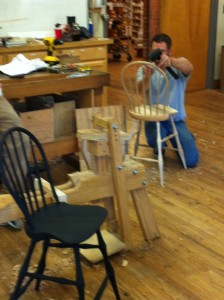
Seat, Legs and Back — Just Some Finish Left
Click here to read about Day 3 of Peter Galbert’s Build a Windsor Chair class.
Or, start at the beginning with Day 1 of Peter Galbert’s Windsor Chair class.