Do you know what it means when something is “redacted”? I think of documents the federal government reluctantly gives up under the Freedom of Information Act where they don’t want you to know what or who they are talking about, so they black out every other word of it and send it to you so they have met the letter of the law but you really don’t know what they are talking about once you see it.
Last year I found a new sales avenue for my Etsy site. I wanted you to know about it, but I don’t want you intruding on my sales so I decided to write about it and then redact it. Here it is.
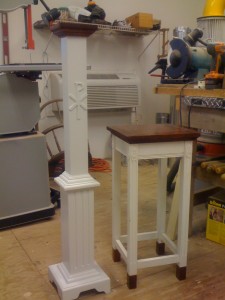
Candle Stand
It turns out there is a pretty good market for we semi-pro woodworkers in the _______ furniture market. This all got started last year when my son graduated from a Master’s program and at his first job decided he needed a candle stand to enhance the services. He and I designed one and I mocked up a couple of them to get the scale right and then made one to match the _______ furniture where he works.
I popped it up on my Etsy site and lo and behold, I sold five more of them all over the country. Actually got tired of making them before it was over. Then last summer, one of the _______ who bought a candle stand wanted me to make an Advent candle stand to match their _______ furniture. That turned out pretty well and they were happy with it. I left it up on the Etsy site and maybe next year I will get some additional sales out of that one too. It is such a thrill to know that _______ all over the country are using my stuff. I’m making two more this season, one for my own _______ and another for a friend up the road who is Pastor of a _______.
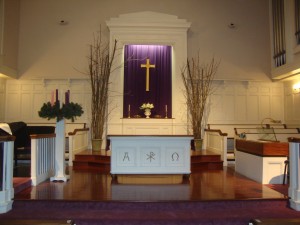
Advent Stand on the Left (Sudbury UMC, MA)
In making the new stands, I found a new router bit. When I make a column of four pieces joined at right angles, a lock joint router bit is the thing to use. These bits cut a joint with a tongue and a slot which fit together when turned at ninety degrees to each other. The joint locks together and is so firm that clamping is almost not necessary. The bit is a little bit touchy to set up correctly and it does require a router table. But man, this thing works like a charm. You can buy it at Highland.
The point of all this is you never know where sales will come from. There is a market out there for your stuff – you just have to find it and work it. Buy more tools, make more stuff, sell it, and buy more tools.