No Southern-fried Southern boy wants to be called a Yankee, but we share the characteristics of shrewdness and thrift. Thus, each month we include a money-saving tip. It’s OK if you call me “cheap.”
A 5 gallon bucket is the perfect diameter for immersing a 10-inch or smaller table saw or circular saw blade in your favorite blade cleaner. I shortened a bucket to about 6″ high, making insertion and removal really easy. Of course, you don’t have to cut down your bucket if you don’t have very many. I’m blessed with tons.
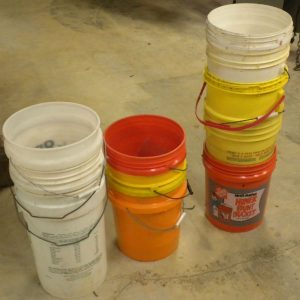
I have some buckets from the “orange” store, and I have some buckets from the “blue” store, but, I’ve never, ever, bought a bucket for use in the shop.
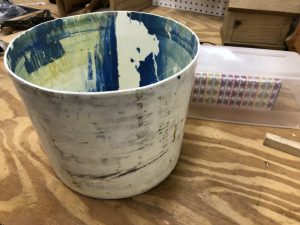
One nice thing about cutting most of the top of the bucket off is easy access. If you put a 10″ saw blade in here, you don’t have to fumble for it at the bottom of a canyon. Another advantage, though, is that it can double as a washing container for parts. Put some solvent in here, grab a toothbrush and some Scotch-Brite pad, and soon your item is clean.
I finally found the ideal (read “free”) soaking container for a 12″ blade. Since I have a 12″ Delta radial arm saw and a 12″ DeWalt miter saw, removing pitch from them meant a lot of scrubbing until I found this bucket on the side of the road, took it home, and discovered it was perfect for soaking our dog’s Potty Park grass, and the lid ideally accommodated a 12″ blade.
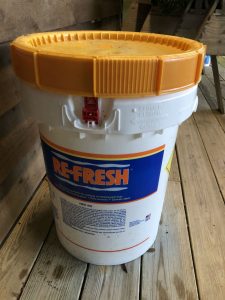
What a find this huge bucket was. It certainly solved two problems for me.
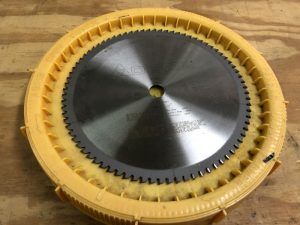
There is just enough diameter, without being wasteful, and just enough depth to fully immerse a 12″ blade.
Now, I warn you, it took years of optically scouring the roadsides before I came across this gem. Don’t think you’re going to
happen on a rare find like this tomorrow. But, maybe I have inspired you to believe, “Yes! It’s really out there waiting for me!”
Jim Randolph is a veterinarian in Long Beach, Mississippi. His earlier careers as lawn mower, dairy farmer, automobile mechanic, microwave communications electronics instructor and journeyman carpenter all influence his approach to woodworking. His favorite projects are furniture built for his wife, Brenda, and for their children and grandchildren. His and Brenda’s home, nicknamed Sticks-In-The-Mud, is built on pilings (sticks) near the wetlands (mud) on a bayou off Jourdan River. His shop is in the lower level of their home.Questions and comments on woodworking may be written below in the comments section. Questions about pet care should be directed to his blog on pet care, www.MyPetsDoctor.com. We regret that, because of high volume, not all inquiries can be answered personally.