No Southern-fried Southern boy wants to be called a Yankee, but we share the characteristics of shrewdness and thrift. Thus, each month we include a money-saving tip. It’s OK if you call me “cheap.”
I hope “those” people never come to visit. Which is probably not a worry, because I live a pretty isolated life: Work, woodshop, church, sleep. Ok, and throw in a little fishing here and there. Entertaining in our home? It’s limited to throwing the raccoon for Willie the poodle and encouraging Maxx the cat to attack him. Willie, that is. Maxx is not interested in the raccoon.
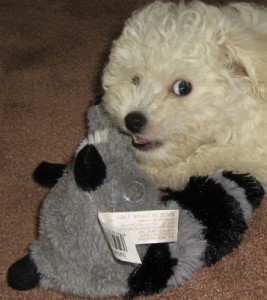
Willie has at least a half-dozen of these “Rocky the Raccoons.” We get them at WalMart. For Christmas Brenda ordered him one from Amazon. He wouldn’t touch it. He wouldn’t even look at it! To him, it’s just not a Rocky
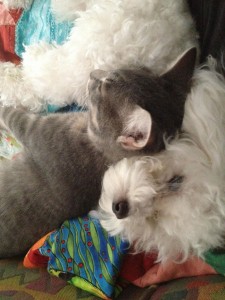
Willie’s favorite toy, however, is his twin brother, Maxx. They’re fraternal twins, which explains their appearance differences.
You want work lights cheap? They don’t come any cheaper than “trash night shopping.” Now that gas is down around $2 per gallon even the driving around is affordable. And, who doesn’t need a night out of the house? Notice the emphasis on “night.” You really do have to watch out for your reputation.
With only our animal entertainment to offer at our house, it’s unlikely that a visitor will show up to identify the two gooseneck lamps I got from their trash one Thursday night. I’m sure they threw them out because they had tightened the thumbscrews as tight as they could and the geese’s “necks” continued to flop around. And, when they did that, they were on the right path, they just didn’t go far enough.
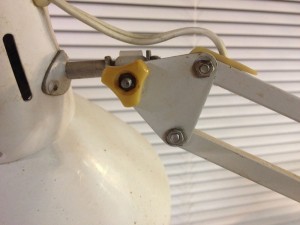
You can tighten this wing nut until your fingers turn white and the lamp will continue to flop if the whole bracket isn’t tight.
The whole idea behind the design of the lamp is friction. Not too much, not too little. Just like the Little Bear’s soup. All it took to make these lights functional for the bandsaw and grinder station is to snug up the other two nuts at each joint. No more flopping around!
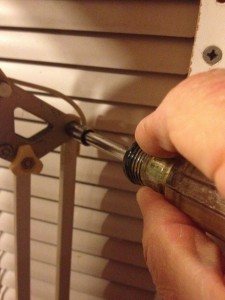
A nut driver is perfect for getting just the right amount of tightness on these nuts because it limits the amount of torque you can apply. No danger of stripping threads.
Sometimes when you find gooseneck lamps in discard piles you won’t find the little plastic base that supports the metal pin. No problem! On the grinder station I just drilled an appropriately-sized hole between the grinders. Now the lamp can turn 360 degrees to illuminate either work area.
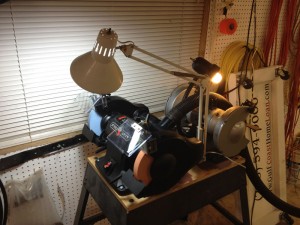
A hole drilled between the grinders works as well or better than the purpose-designed plastic mounting block.
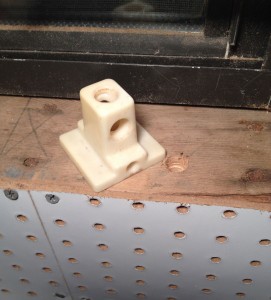
Good luck finding the plastic bracket in the trash with the discarded lamp, but they can be handy sometimes.
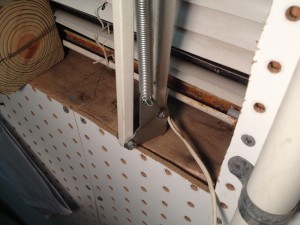
Not wanting to drill a hole in the bandsaw’s table, I mounted the lamp in the windowsill and it works great.
—
Jim Randolph is a veterinarian in Long Beach, Mississippi. His earlier careers as lawn mower, dairy farmer, automobile mechanic, microwave communications electronics instructor and journeyman carpenter all influence his approach to woodworking. His favorite projects are furniture built for his wife, Brenda, and for their children and grandchildren. His and Brenda’s home, nicknamed Sticks-In-The-Mud, is built on pilings (sticks) near the wetlands (mud) on a bayou off Jourdan River. His shop is in the lower level of their home. Questions and comments on woodworking may be written below in the comments section. Questions about pet care should be directed to his blog on pet care, www.MyPetsDoctor.com. We regret that, because of high volume, not all inquiries can be answered personally.