Over the past year I have learned that the world of woodcraft is populated with more tools than there are trees in Georgia. Everywhere I look, I find a tool for this and a tool for that with multiple types of tools for this and that. Take something as basic as cutting wood. Your options are a handsaw, bandsaw, circular saw, table saw, chainsaw, chop saw, miter saw… The cheapest option to start with is the handsaw, but then you get to decide if you need a back saw, fret saw, coping saw, jab saw, frame saw, hack saw, etc. Before too long, you begin to feel like Bubba in Forest Gump rattling off shrimp recipes.
Livin’ On a Prayer
Completely lost as to what tools I really needed, I looked to YouTube for help. A quick search returned a seemingly endless list of videos with titles like 5 Woodworking Tools for Beginners, 6 Essential Woodworking Tools for Beginners, 26 Basic Woodworking Tools for Beginners and so on. Since I really wanted to get started, but I wasn’t fully committed to woodworking, I started with the list of 5 tools. A few hundred dollars lighter, I had my tools and set to working up my first project plan. I started drawing my first flower box with a pen, paper, and an old notebook I had left over from college that wasn’t entirely filled with notes about ancient Greece. After about an hour of scribbling and pulling measurements out of thin air, I confidently marched to the garage and began cutting up the 2 and 4x4s the previous homeowner had generously left behind. With enough wood to piece together the first box I soon realized a foot is a good measurement for a sub sandwich, and not so good for a flower box meant to support a 4×4 with a string of lights attached to the top of it. Back to the drawing board.
Is This Love
In hindsight, I am glad I made such an extreme blunder with my first design. Had it just been a little off, I would have proceeded along with the build and done what I could to make it work; likely ending up with a mess on my patio when the first serious thunderstorm blew through. Since it was so far off as to be unusable, it lead to me discovering what I now consider to be the most important tool for any beginning woodworker – Computer-Aided Design or CAD software.
Historically (and even now), CAD software has been synonymous with professional level usage in architecture, engineering, and construction sporting a price tag well into the thousands of dollars. Around two decades ago, a small startup named @Last Software released a 3D modeling program named SketchUp for the relatively cheap price of $495. In 2006, a larger startup named Google purchased @Last and released a free version of SketchUp. The rest is digital history, but the major disruption to the CAD world was the democratization of CAD software. Even the CAD juggernaut Autodesk now offers free software for hobbyists. Nothing else I’ve purchased has had a greater impact on every aspect of woodworking as my CAD programs have. There really ought to be a YouTube video titled 1 Basic Woodworking Tool for Beginner Woodworkers essentially that stresses the value and importance of using CAD in woodworking.
Nobody Rides for Free
I have one of those virtual assistants in my garage shop that doubles as jukebox. I call her Siri or Alexa. While I work, I listen to random playlists. Movie scores for glue ups, electronica (techno!) for routing and hair metal for sawing. I guess because of the Geico commercial that came out last year RATT had a bump in popularity on the curated playlists which eventually found their way into my shop playlists. All of this to say that Nobody Rides for Free, in my opinion, really should be considered the anthem, or at least motto, for every woodworker out there. At every turn with woodworking it costs money. Heck, even turning is expensive when working with wood! Wood prices are at all time highs; tool prices are going up after a Covid induced price freeze; regular consumables like shop towels, sandpaper, blades, stain, etc. all add up quickly. Nobody rides for free indeed! As with every rule there is always an exception, and the only one I’ve found in woodworking is my CAD software. It helps me visualize, prototype, measure, cut, glue, stain all without spending a dime on a board of lumber or sheet of sandpaper. When I take these digital dreams into reality, I know exactly what consumables and tools I will need to realize my grand vision of an oak cutting board with a strip of walnut in the middle.
Look What the Cat Dragged In
The two most popular programs I’ve found are SketchUp and Fusion 360. I started in SketchUp last year and picked up Fusion 360 a couple of months ago. Both offer free versions, both are easy to start basic designs with, and both produce a 3D model of what I’m building. How they get me from a blank X, Y, Z axis to a final model is wildly different. Pricing is similar for both. SketchUp has a free version that is entirely web based so while you listen to the latest The Highland Woodworker episode in this window you can start building your first 3D model in the tab next to it. Fusion 360 is a full desktop program where you certify at sign up that you are a hobbyist working on personal projects and, in turn, get the software for free. There are paid versions as well that I’m sure I’ll write about another time, but the free ones are enough to get started.
The major difference between the two is how you design projects: SketchUp uses direct modeling and Fusion 360 uses parametric modeling. Which workflow is easiest to pick up really depends on whether you were an A or C student in high school math. I was a D student, so SketchUp was much easier for me to get up and running in. If I want a board of a certain size, I just draw it. Then draw another and another and another and so on. It’s a lot like physically working with wood in a shop where your mouse replaces a tablesaw.
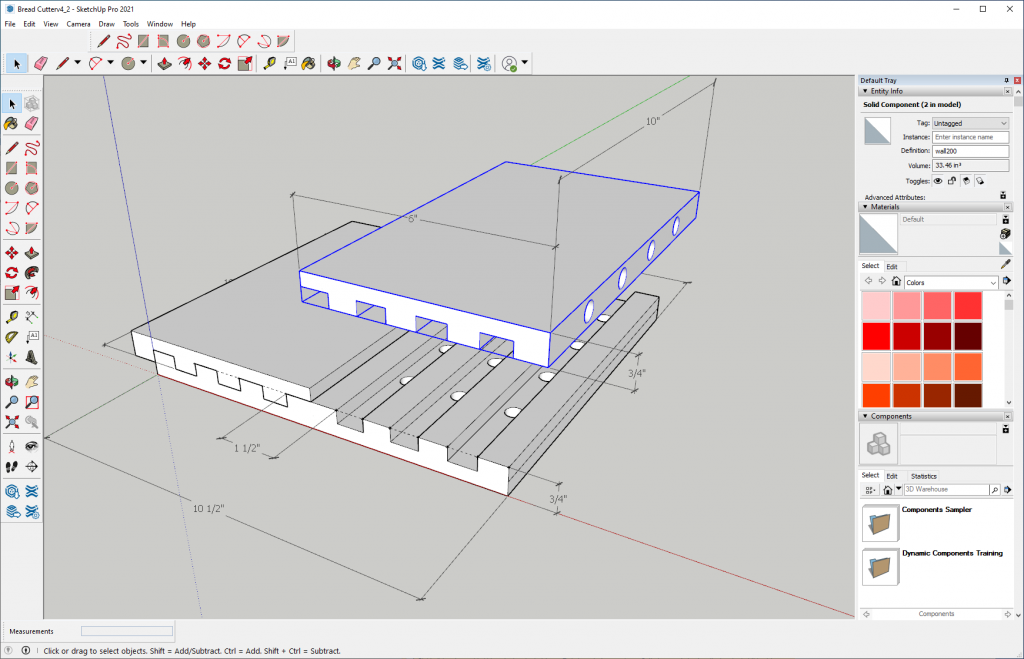
On the other hand, Fusion 360 works best by building parameters around a board and writing formulas to assemble those boards into a complete piece. There is a degree of direct modeling you can do, but it’s not as friendly as it is in SketchUp. Where it really shines is when you are building larger projects with a lot of boards. Using the parameters and formulas you’ve developed, it takes no time to assemble a design, adjust sizes, join pieces, export for CNC, etc.
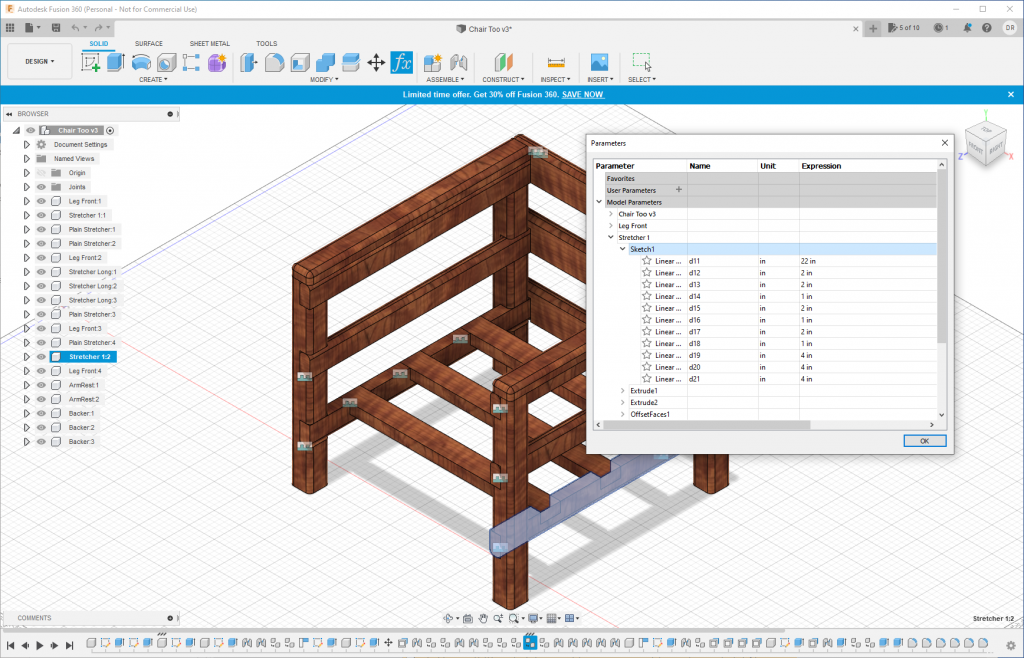
As of this writing, I use SketchUp to take the chicken scratch I call drawing into the 3D world. Once there, I can play around with size, shape, fit, color, etc. without wasting money on wood and consumables. Once the design in SketchUp is finished, I open Fusion 360 and start building the same project there. I’ve found duplicating projects in both programs has really accelerated my trip up the learning curves of both programs. Even better, a natural feedback loop has developed where once I learn something in one program I then figure out how to do it in the other.
Every Rose has Its Thorn
My first project in SketchUp took weeks to finish. It became so frustrating at times that I would give up for stretches of days and sulk rather than spend the energy trying to find out if I was going about this the wrong way. In my mind, I had watched the equivalent of a semester’s worth of videos on how to use SketchUp so I should be well versed in how to use it. Much like my notes from the course on ancient Greece I took in college, all of the information was there, but I couldn’t begin to tell you what the Ionian Revolt was about other than an educated guess that it involved the Greeks and the Ions. My Icarian approach was not working. I had done all of the research and studying, my head jam packed with things like offset, orbit, pan, but it was really just a lukewarm term soup.
My breakthrough occurred when I gave up on the flower box I wanted to design and started over building a simple useless box. Unsurprisingly, googling ‘SketchUp box’ returns a number of videos that walk you through this Herculean task. Once I had found one I liked, I cued it up on my phone and opened SketchUp on my computer. I followed along, pausing and rewinding when something wasn’t working, and like a mindless mimic managed to build my first 3D box. I paused the video, deleted the file and started over. When I got stuck, I’d pull up the video and replay that section. What seemed nearly impossible to accomplish with consistency gradually became a walk in the park. After that I started experimenting with building a box of different dimensions, different joinery, stacking boxes to make bigger boxes, adding boxes inside boxes to make drawers, and so on until I felt I was reasonably capable of revisiting my flower box project. By that time, I had become so comfortable using the basics of SketchUp, that I ended up building a dimensionally accurate version of my patio to see how I should run the string lights and what the whole thing would look like.
Home Sweet Home
I am predominantly a visual learner. If I see something, I can say something. If I read something, I’m going to need a lot of repetition throughout to really pick it up. I know this post is a lot longer than I intended, but I felt it was incredibly important to write and write again how critical CAD software is to woodworking. There is no tool on the market that can beat its price, its countless uses, and its safety. You will never accidentally cut off a finger using a CAD program to cut up a 4’x 8’ sheet of plywood. I am sure there are people working in furniture design today that have never seen the inside of a woodshop, but you can find their furniture flat packed and ready to assemble at your local Target or Wal-Mart. There are already 3D printers on the market that can build objects using wood based filament so it’s entirely possible a new generation of woodworkers will arise where their only tools are a CAD program and a printer.
But I like the feel of a board moving smoothly against a sharp saw, the smell of fresh woodchips, the sharp whine of a power tool and I feel real good because I am a craftsman and that means I can use my mind and my hands to create. Of course, I don’t know if I’d ever tell my buddies all of this because sometimes they laugh when you tell them things like this. So whether you are a digital dodo or evangelist; whether your power comes from the Southern Company or a waterwheel and horse; learning a CAD program today will give you the plan and path to build with any tool from the past, present and future.
Based in Atlanta, Travis can’t draw a straight line, cut a board or drill a hole without a healthy flow of electrons. Follow along as this lifelong video game enthusiast, professional introvert, and one time IT virtuoso leaves behind cyberspace for a hybrid world where binary fuses with boards to create a digital woodspace. You can contact him at digitalwoodspace@gmail.com.
I find this whole thing rather strange, I, and a lot have been building stuff for years with out a computer. If you can’t do that without a computor to figure out stuff, what is the point?
I will admit I just skim read the article, so maybe missed the point.
I agree with Barry! Been doing various projects for over forty years without computer help.
That’s the fun of it! All the tech stuff coming in nowadays seems to take too much individuality away from projects. I have always liked the small things that make them one of a kind. As I used to tell my students, if you want perfection w/o an odd mark or two, go buy it at the dime store. Amg
Just because the author uses a computer to draw out and work through designs doesn’t make it inferior— why not be supportive that there are more and different people interested in woodworking? One method is not better than another. There’s room for it all.